9S 칼리버에 더 대해 알아보기
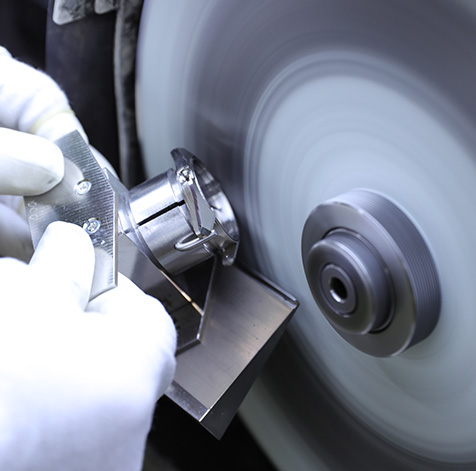
수십년에 걸쳐 완성된 예술, 자라츠(Zaratsu) 폴리싱
자라츠 폴리싱에서 장인은 연마할 표면을 회전하는 원반 전면에 대고 누릅니다. 원반은 물론 균일한 속도로 회전하지만 연마기는 원반이 중심보다 가장자리에서 더 빨리 움직이는 사실을 이용하여 원하는 왜곡 없이 처리할 수 있습니다. 케이스의 표면을 원반 중심 쪽으로 또는 멀어지게 이동시켜 매우 미묘하면서도 정확한 표면과 가장자리를 만들 수 있습니다. 가해지는 압력이나 케이스를 잡는 각도의 미세한 차이에도 케이스의 외관이 바뀝니다. 각각 경우에 똑같은 효과를 재현하려면 고도로 숙련된 베테랑 장인의 기술이 필요합니다. 이 자라츠 공정에 사용되는 연마 기계는 반세기 전에 외부 공급업체에서 가져온 것이지만 이제는 Seiko만의 전용 연마 기계로 완벽하게 개량되었습니다. 이 새로운 기계는 작업자가 원반의 회전 수를 각 작업에 가장 적합한 수준으로 설정할 수 있는 능력을 포함하여 더 높은 사양과 향상된 기능을 갖추고 있습니다. 장인들은 또한 스테인리스 스틸과 고강도 티타늄 표면 모두에서 잘 작용되기 위해 그랜드 세이코 팀이 수많은 시행착오 끝에 개발한 폴리싱 컴파운드를 사용합니다.
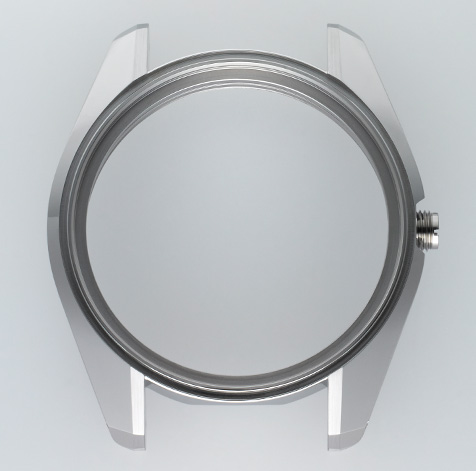
가공되지 않은 금속에서 시계 완성품까지의 긴 여정
9S 칼리버 무브먼트가 장착될 모든 케이스는 먼저 300톤의 냉간 단조 프레스로 성형됩니다. 그런 다음 케이스를 섭씨 1,000도 이상의 온도에서 반복 열처리를 통해 여러 개의 다이를 사용하여 세부 사항을 점차적으로 성형합니다. 그런 다음 CNC(컴퓨터 수치 제어) 기계를 사용하여 추가 개선 프로세스가 이뤄집니다. 아마도 "기계에 의한 금속조각(Metal Sculpting by Machine)"이라고 해야 할 것입니다. 정밀 가공의 각 단계는 주조한 케이스 표면의 약 0.1mm를 벗겨냅니다. 마지막 공정은 연마입니다. 각 디자인에는 각각의 프로필(개요)이 있지만 평균 50개의 개별 연마 과정이 필요합니다. 이 공정의 마지막 단계에서 두 번째 단계가 거울처럼 마감처리하는 자라츠 폴리싱입니다.
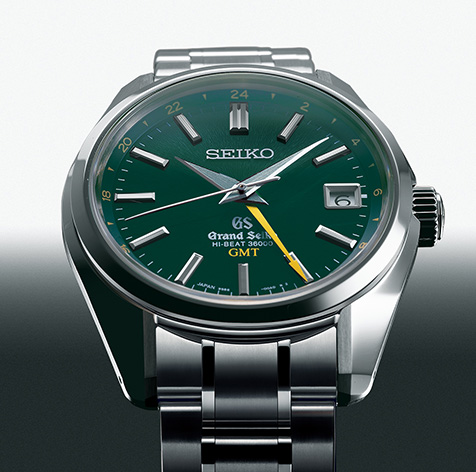
쁘띠 에귀유 상(The Petite Aiguille award)
2014년 10월. 제네바 시계 그랑프리에서 그랜드 세이코의 기계식 Hi-Beat 36000 GMT Limited Edition이 쁘띠 에귀유(Petite Aiguille) 상을 수상했습니다. 9S86 무브먼트가 장착된 이 시계는 같은 해 초 일본 정부로부터 현대 장인 칭호를 받은 Nobuhiro Kosugi가 디자인했습니다. 무브먼트는 이와테 현의 시즈쿠이시 워치 스튜디오에서 조립되었고 케이스는 후쿠시마의 공장에서 제조되었습니다. 특히 이 지역은 2011년 도호쿠 지진시 큰 피해를 입었는데, 이 상이 모든 장애물을 극복하려는 워치메이킹의 기량과 결의에 대한 결과물로 큰 찬사를 받았습니다.