为什么我们需要超镜面研磨?
1960年代后期负责Grand Seiko的设计师建立了”SEIKO Style”这套设计规范。当时日本腕表在瑞士天文台举行的精准度竞赛中拿下了优秀的名次,而这套设计规范的存在是为了要让我们的表款除了精准度之外,在设计和完成度上也能展现出耀人的光彩。最早体现了这套美学的是67年推出的44GS以及来年的61GS这两款Grand Seiko,两款分别是由当时的第二精工舍(现为SEIKO Instruments Inc. )和诹访精工舍(现为SEIKO Epson)所制作,乃是Grand Seiko机械表款历史中的名作。
SEIKO Style的设计以平面为主,要求将外装的切面打磨成工整的超镜面;时标和指针同样采用了大面积的平面,让使用者即便在微光下也能轻松读取时刻。设计师经常在生产现场与当时的职人们一同摸索加工技术的可能性,在经历了无数的反复尝试后,SEIKO Style终于正式确立,而这套设计往后也成了所有负责Grand Seiko的设计师持续沿用的规范。话虽如此但这套规范并非限制设计的框架,而是指出设计目的与方向的方针,每位设计师都会根据自身的美学和方法论来对SEIKO Style加以诠释,由此创作出全新的Grand Seiko。
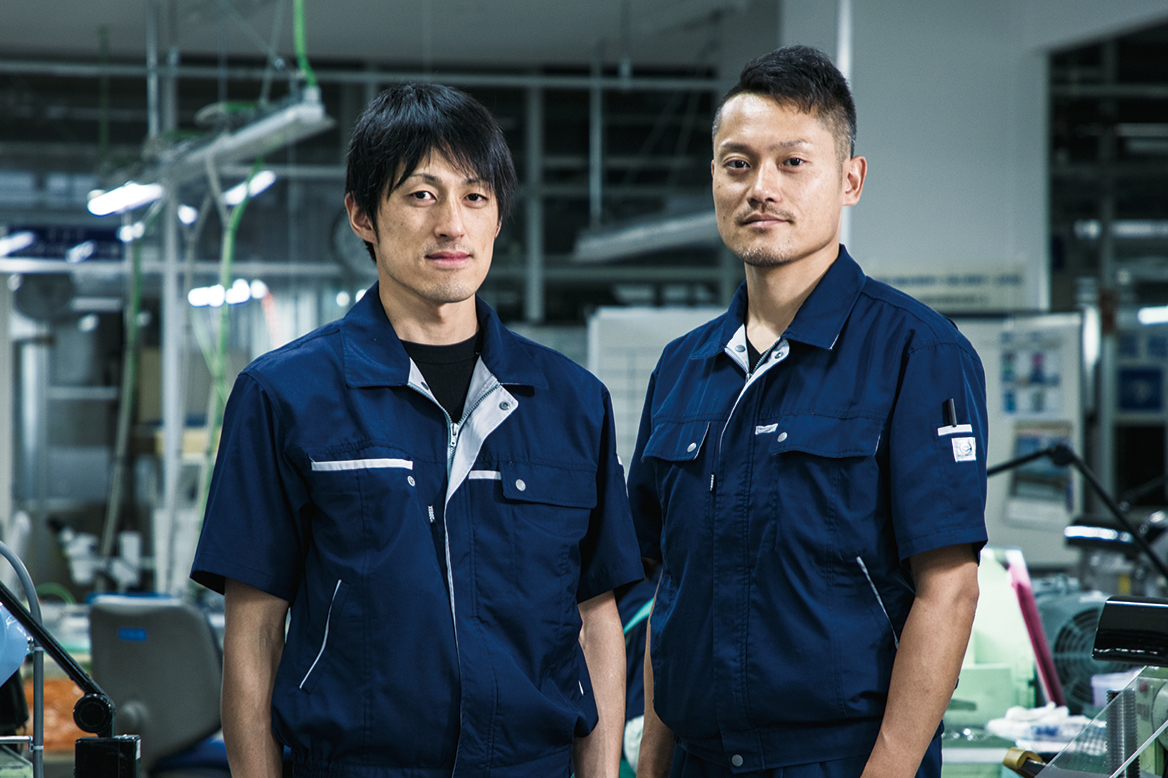
要完成具备SEIKO Style的Grand Seiko各方面都必须倚赖高超的职人技巧,而「超镜面研磨」正是其中之一。镜面抛光与发丝纹打磨的基底要先经过打磨工序做出「超平滑表面」,而对于像SEIKO Style这种要求面与面相交成锐利棱线的情况来说前期的打磨尤其不可或缺。镜面抛光的「布轮打磨」这个动作无可避免地会把棱线的「锐角」给磨圆,因此这里我们必须尽可能地缩短布轮打磨的时间,而要维持表壳犀利的造型,超镜面研磨更是必要的前端工序。
Grand Seiko的表壳一开始会先以NC(自动切削加工)或是冷间锻造其中一种方式成型,两者之间的差异在于一种是像雕刻一样雕出造型、另一种则是以数百顿的压力加压成型。过去这个阶段的工序精密度不高,成型后还要处理毛边,尽管随着技术的进步相关工序的精密度如今已有了戏剧性的提升,但要完成一个表壳还是得仰赖后续职人的巧匠手艺。成型后透过平板打磨和布轮粗磨去除表壳表面的凹凸,接下来就进入了超镜面研磨的阶段。
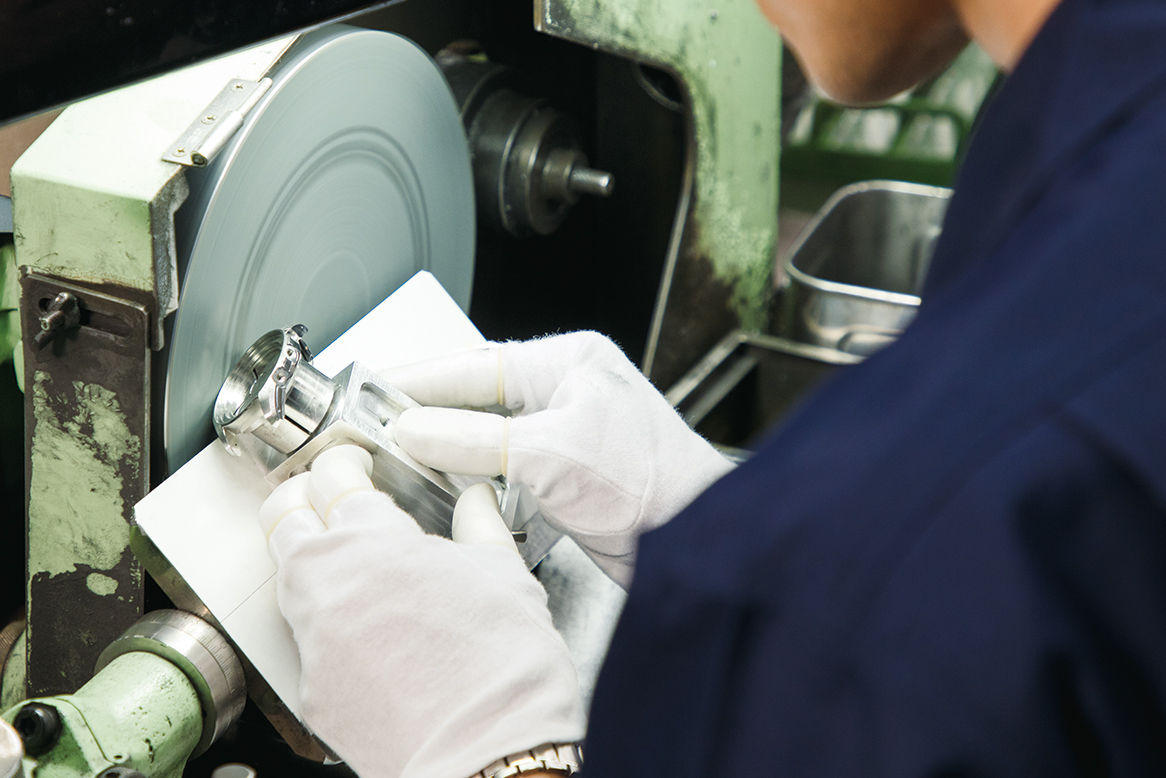
“Sallaz”是以前瑞士一间设备机具商的名字,后来日本的打磨职人索性将有用上这间公司某一型打磨机具的工序直接称作「Sallaz研磨」或是「超镜面研磨」。职人启动贴着研磨纸的铝制转盘,将表壳的研磨面从正面(而非侧面)抵在转盘上移动,透过这道工序将金属面打磨成超平面。虽然接下来还会再用收尾的布轮抛出镜面,不过要是少了之前超镜面研磨的工序,后续不论再怎么抛光表面都还是会有歪斜。超镜面研磨的作工好坏取决于表壳抵住转盘时的力道强弱、打磨时间以及滑动速度等等要素,凡此要素全由打磨职人的手感所左右。
隶属于信州 时之匠工房里的「表壳工房」,超镜面研磨职人黑木友志说到,「超镜面研磨的难处在于抓到平衡感。即使某个部分做得很好,左右表耳切面的形状也常常会有微妙的不同。所以不能只是一个部分一个部分慢慢磨,而是要加强表壳压在转盘上的力道,一边观察整体状况一边快速地完成。之前我也是花了好几个月才让身体记住这个诀窍」